Metallic stearates are a group of metal salts derived from stearic acid (a long-chain fatty acid) that play a critical role in improving the properties and processability of plastics. The most common metallic stearates include calcium, zinc, magnesium, aluminum, and barium stearates.
Roles and Effects of Metallic Stearates in Enhancing Plastic Properties:
- Lubricant:
- Metallic stearates reduce friction between the polymer and mold or equipment surfaces, improving polymer flowability.
- This lubrication helps lower energy consumption, prevents sticking of the polymer to mold surfaces, and extends equipment life.
- Mold Release Agent:
- In molding processes (such as injection or compression molding), these materials prevent polymers from sticking to the mold, facilitating easier demolding.
- Heat Stabilizer:
- Some stearates (such as calcium and zinc stearates) act as heat stabilizers, especially in PVC, preventing degradation of polymer chains at high temperatures.
- They inhibit the formation of HCl in PVC, which would otherwise accelerate degradation.
- Improvement of Surface Properties:
- Stearates enhance surface gloss, reduce tackiness, and improve the tactile feel of plastic parts.
- Antistatic Agent:
- Certain stearates help reduce dust attraction by lowering surface static, thus improving the electrical surface properties of plastics.
- Filler Dispersant:
- Especially in filled compounds (such as those containing talc, calcium carbonate, etc.), stearates improve the dispersion of filler particles in the polymer matrix.
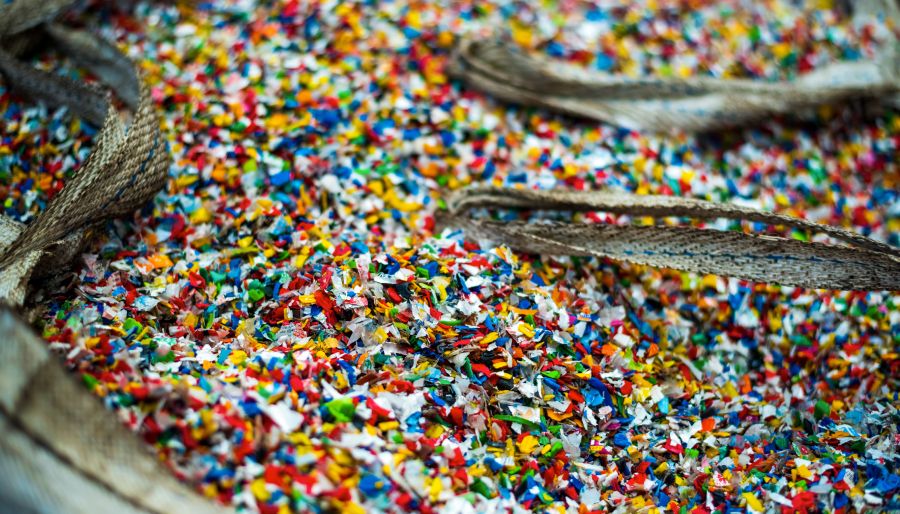
Comparison of Different Types of Metallic Stearates in Plastic Applications
- Calcium Stearate
- Function: Heat stabilizer, internal lubricant
- Applications: Rigid and flexible PVC formulations, rubber and paint industries
- Key Feature: Non-toxic, suitable alternative to lead-based stabilizers
- Zinc Stearate
- Function: External lubricant, mold release agent
- Applications: Injection molding, foams, paints, and molding powders
- Key Feature: Enhances surface gloss, aids in filler dispersion
- Magnesium Stearate
- Function: Lubricant, anti-blocking agent
- Applications: Plastics, pharmaceuticals, masterbatches
- Key Feature: Reduces sticking during extrusion processes
- Aluminum Stearate
- Function: Thickener, water repellent
- Applications: Paints, plastics, adhesives
- Key Feature: Heat-resistant, compatible with non-polar systems
- Barium Stearate
- Function: Strong heat stabilizer
- Applications: Rigid and semi-rigid PVC, cables and wires
- Key Feature: Long-term stability, resistant to light and heat
The roles and effects of metallic stearates in enhancing plastic properties have gained significant attention in the polymer industry, as these compounds function simultaneously as heat stabilizers and lubricants, thereby facilitating the production process. Stearates such as calcium, zinc, and barium stearates reduce friction between polymers and processing equipment and prevent premature thermal degradation of the polymer. Moreover, their impact is clearly observed in improving surface gloss, increasing thermal resistance, and enhancing the uniformity of the final product structure.
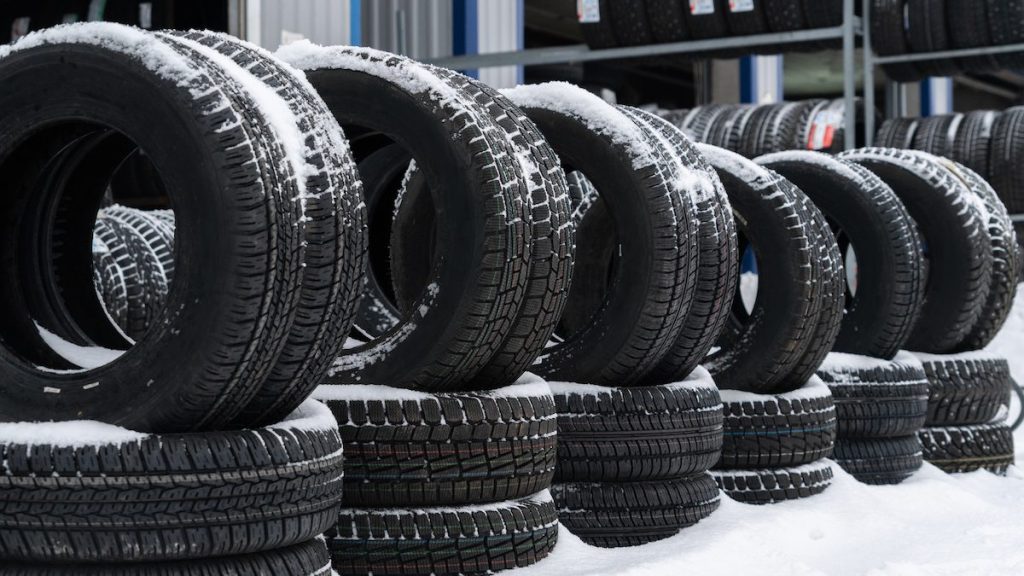
Read more: