PVC, or polyvinyl chloride, is one of the most popular and versatile polymers globally. However, like all polymers, PVC is not immune to degradation during processing and over its life. Heat, light, and other environmental factors can degrade PVC, leading to discoloration, loss of mechanical properties, or even complete failure. To fight this degradation, manufacturers use stabilizers. Among the wide range of stabilizers available, methyl tin stabilizers have emerged as one of the most effective, particularly for clear, rigid PVC applications. This article delves into the importance, usage, and benefits of methyl tin stabilizers in PVC applications.
1. Introduction to Stabilizers in PVC
PVC is a unique polymer. In its raw state, it’s brittle and rigid. Manufacturers add plasticizers to make PVC flexible and use stabilizers to enhance its resistance to heat and light. Stabilizers prevent the breakdown of PVC during high-temperature processing and prolong its life during usage.
There are various types of stabilizers, including:
- Lead-based stabilizers
- Calcium-zinc stabilizers
- Barium-zinc stabilizers
- Tin-based stabilizers (like methyl tin stabilizers)
Each stabilizer has its own advantages and limitations, and the choice depends on the application, processing conditions, desired properties, and regulatory compliance.
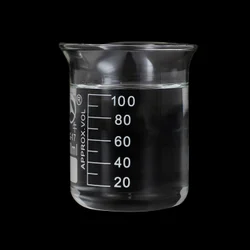
2. Methyl Tin Stabilizers: An Overview
Methyl tin stabilizers are organotin compounds that have proven to be the most efficient stabilizers for PVC, especially for clear, rigid PVC applications like bottles, sheeting, and medical equipment.
There are typically two types:
3. Why Use Methyl Tin Stabilizers?
a. Superior Thermal Stability: PVC can degrade when subjected to high temperatures during processing. Methyl tin stabilizers provide superior heat stability, ensuring the PVC retains its desired properties during and after processing.
b. Excellent Transparency: For applications where clarity is crucial, such as in food packaging or medical tubing, methyl tin stabilizers are unmatched. They ensure that the finished product remains clear and free from haze or discoloration.
c. Regulatory Approval: Methyl tin stabilizers are approved for use in food contact and potable water applications in many countries, making them ideal for products like water bottles or food packaging.
d. Improved Weatherability: These stabilizers can enhance the UV resistance of PVC, ensuring that products don’t discolor or degrade under sunlight.
4. Application Areas
Methyl tin stabilizers are predominantly used in:
- Food Packaging: Bottles, containers, and food wraps benefit from the clarity and non-toxicity provided by these stabilizers.
- Medical Equipment: PVC medical devices like tubing, IV bags, and other equipment require utmost clarity and safety. Methyl tin stabilizers ensure that these products remain stable and safe during their lifecycle.
- Construction Materials: PVC window profiles, doors, and other construction materials benefit from the UV resistance and durability offered.
5. Environmental and Safety Concerns
Though methyl tin stabilizers offer numerous advantages, there are concerns about their environmental impact. The use of tin in various applications has led to its detection in environmental samples. Therefore, it’s crucial to ensure that PVC products with these stabilizers are properly disposed of.
Also, while they are approved for many applications, manufacturers must still adhere to recommended limits and guidelines, ensuring products remain safe for end-users.
6. Conclusion
PVC is an indispensable polymer, and to harness its full potential, the right stabilizers are paramount. Methyl tin stabilizers, with their unparalleled heat stability, clarity, and safety profiles, have proven to be an invaluable tool in the PVC industry. As we continue to prioritize sustainability, it’s vital to also focus on the proper use and disposal of PVC products to minimize environmental impact. Manufacturers, researchers, and policymakers must collaborate to ensure the safe and sustainable usage of these invaluable compounds.